CNC Lathe Part Factory: Excellence in Metal Fabrication
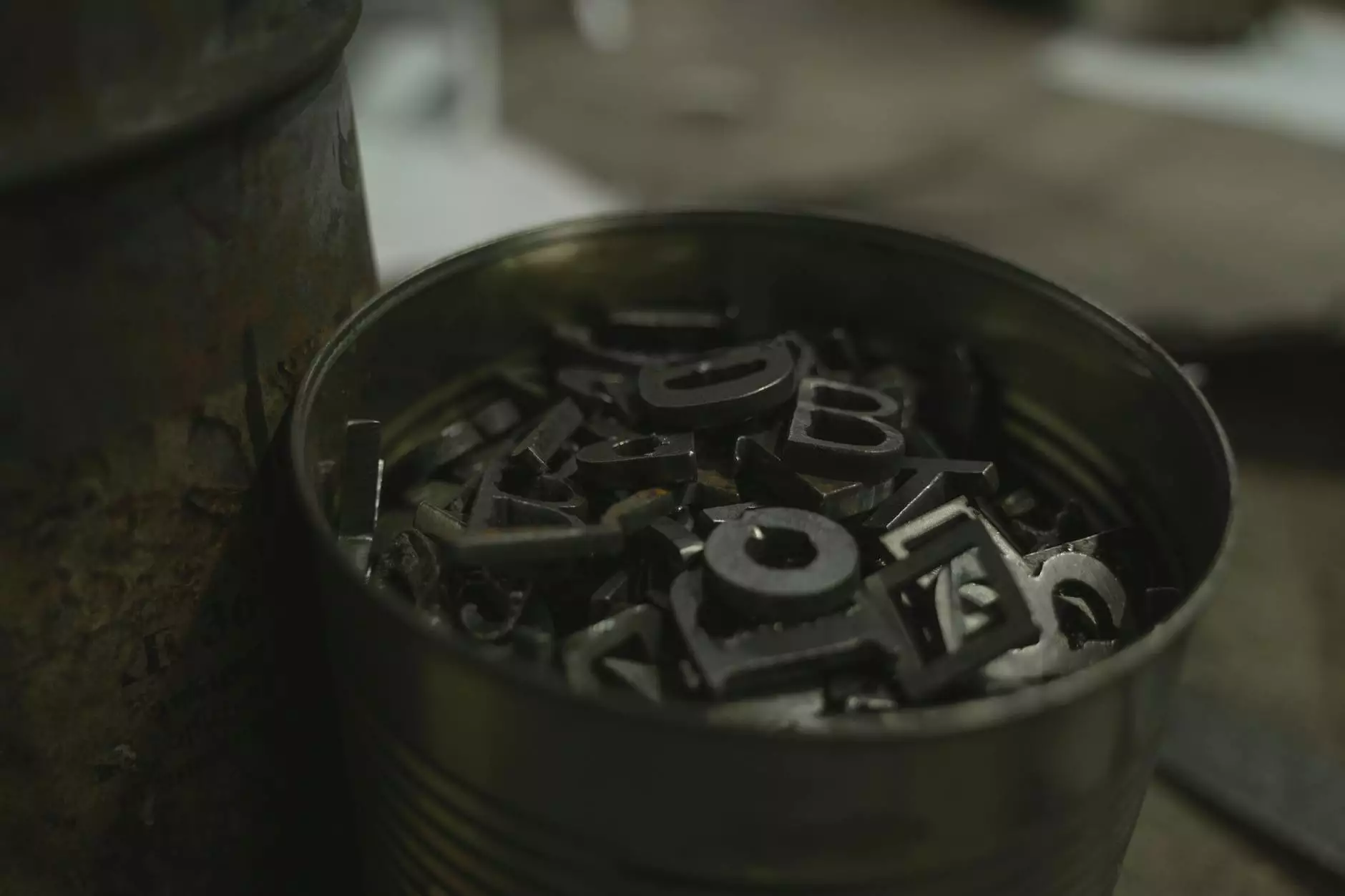
In today's rapidly evolving manufacturing landscape, understanding the significance of a CNC lathe part factory is paramount. This article delves deep into the intricate workings, advantages, and contributions of these factories to the metal fabrication industry. As businesses increasingly depend on precision and efficiency, a factory that specializes in CNC lathe parts becomes essential in driving productivity and quality.
What is a CNC Lathe Part Factory?
A CNC lathe part factory is a specialized manufacturing facility that utilizes Computer Numerical Control (CNC) technology to perform machining processes on various materials. These factories are equipped with advanced machinery designed to produce complex shapes and components with a high degree of precision. CNC lathes allow for automatic control of tool movements, drastically improving efficiency and accuracy in production.
Understanding CNC Technology
CNC technology revolutionized metal fabrication by facilitating automated operations that were traditionally labor-intensive. Here are some key components of CNC technology:
- CNC Machines: These machines execute predetermined sequences based on uploaded computer programs, allowing for intricate design and precision.
- Software: CAD (Computer-Aided Design) and CAM (Computer-Aided Manufacturing) software play crucial roles in the design and execution of machine operations.
- Tooling: Specialized tools are used to create precise cuts and shapes on various types of materials, enhancing versatility in production.
The Role of CNC Lathe Part Factories in Metal Fabrication
CNC lathe part factories cater to a variety of industries by providing essential components. The versatility of CNC machining allows for the production of parts that serve multiple functions across different sectors, such as:
- Aerospace: Precision components for aircraft and spacecraft.
- Automotive: Engine parts, transmission components, and structural elements.
- Medical Devices: Components for surgical instruments and diagnostic equipment.
- Electronics: Parts for devices such as smartphones and computers.
Advantages of Choosing a CNC Lathe Part Factory
The adoption of CNC technology in manufacturing has brought numerous advantages that enhance production and quality. Let’s explore some of these benefits in detail:
1. High Precision and Accuracy
One of the most significant advantages of using a CNC lathe part factory is the ability to produce parts with exceptional precision. CNC machines are programmed to follow exact specifications, which minimizes human error and ensures that every part meets rigorous tolerances.
2. Increased Production Efficiency
The automation of processes in CNC machining leads to increased productivity. Once programmed, CNC machines can operate continuously, reducing the time required for manual interventions. This allows factories to produce larger quantities of parts in shorter timeframes, meeting customer demands effectively.
3. Versatility in Production
CNC lathe part factories are capable of working with a wide range of materials, including metals, plastics, and composites. This versatility allows for the production of diverse components, catering to different industry needs without requiring extensive reconfiguration of machinery.
4. Consistency in Quality
With CNC technology, the consistency of quality is significantly enhanced. Each part produced is identical to the previous one, ensuring reliability and uniformity across multiple production runs. This is crucial for industries where part compatibility is vital.
Key Processes in a CNC Lathe Part Factory
The operation of a CNC lathe part factory involves several key processes that contribute to the overall production workflow. Understanding these processes is essential for grasping how factories achieve such remarkable levels of quality and efficiency:
1. Design and Prototyping
The manufacturing process starts with designing parts using CAD software. Engineers create detailed models that serve as templates for production. Prototyping is often conducted to test designs before full-scale production.
2. Machine Programming
Once a design is finalized, it’s converted into a machine-readable format. This programming dictates the movement of tools and the operation of the CNC lathe, ensuring that the machine executes the desired cuts with precision.
3. Material Selection
Choosing the right material is crucial. Factors such as strength, weight, and corrosion resistance play significant roles in the selection process. A CNC lathe part factory offers the capability to work with various materials based on project specifications.
4. Machining Operations
This is the core of the CNC lathe part factory workflow. The lathe executes operations such as turning, facing, boring, and threading, transforming raw materials into finished components. Monitoring and fine-tuning during this stage are essential to maintain quality.
5. Quality Control
After machining, parts undergo rigorous quality control inspections to ensure they meet industry standards and customer requirements. Techniques like dimensional analysis and surface finish assessments are employed to guarantee flawless execution.
Future Trends in CNC Lathe Part Factories
The landscape of manufacturing is continuously evolving. Several trends are shaping the future of CNC lathe part factories, paving the way for innovation and enhanced efficiency:
1. Integration of IoT
The Internet of Things (IoT) is becoming increasingly integrated into manufacturing processes. Smart factories equipped with IoT devices offer real-time data tracking and analytics, allowing manufacturers to optimize operations and predict maintenance needs before issues arise.
2. Advanced Materials
As the demand for higher-performance components grows, the use of advanced materials such as carbon fiber and titanium is increasing. CNC lathe part factories are adapting to work with these materials, offering strength and lightweight solutions for various applications.
3. Automation and Robotics
Automation enhances efficiency further by integrating robotics into the production line. Robots can handle repetitive tasks such as loading and unloading, freeing up human workers to focus on more complex operations.
4. Sustainability Practices
With growing concerns over environmental impact, many CNC lathe part factories are implementing sustainable practices. This includes reducing waste, recycling materials, and utilizing energy-efficient operations to lower their carbon footprint.
Choosing the Right CNC Lathe Part Factory
When looking for a CNC lathe part factory, consider the following factors to ensure you make an informed decision:
- Expertise: Investigate the factory’s experience and specialties in your particular industry.
- Technology: Assess the type of CNC machines and technologies used in the factory. Advanced machinery often contributes to higher quality production.
- Quality Assurance: Review the factory's quality control processes and certifications to ensure they meet industry standards.
- Customer Service: Reliable communication and customer support are crucial for successful collaboration.
The Impact of CNC Lathe Part Factories on Business
The impact of a CNC lathe part factory extends far beyond just manufacturing. Their influence permeates multiple layers of business operations:
1. Enhancing Product Development
Quick prototyping capabilities facilitate faster product development cycles. Businesses can test designs and iterate on them more rapidly, allowing them to bring products to market quicker than competitors.
2. Cost Efficiency
By employing CNC technology, manufacturers can minimize material waste and reduce labor costs. This cost efficiency directly contributes to healthier profit margins, enabling businesses to reinvest in growth.
3. Competitive Advantage
A reliable CNC lathe part factory can serve as a competitive advantage. High-quality, precision parts can differentiate a business in crowded markets, enhancing brand reputation and customer loyalty.
4. Supply Chain Optimization
Effective partnerships with CNC lathe part factories can streamline the supply chain, improving responsiveness and reducing lead times. This agility is vital in today’s fast-paced business environment.
Conclusion
In conclusion, a CNC lathe part factory plays a crucial role in the metal fabrication industry by providing precision, efficiency, and versatility to manufacturers across multiple sectors. As technology continues to evolve, these factories are poised to embrace new trends, enhancing their capabilities and ensuring that they meet the ever-growing demands of businesses.
By understanding the advantages and functions of a CNC lathe part factory, businesses can make informed decisions that drive their growth and success in a competitive landscape. Leveraging the capabilities of these factories not only enhances operational efficiency but also contributes significantly to product success and market leadership.