Understanding Injected Molded Plastic: Transforming the Manufacturing Landscape
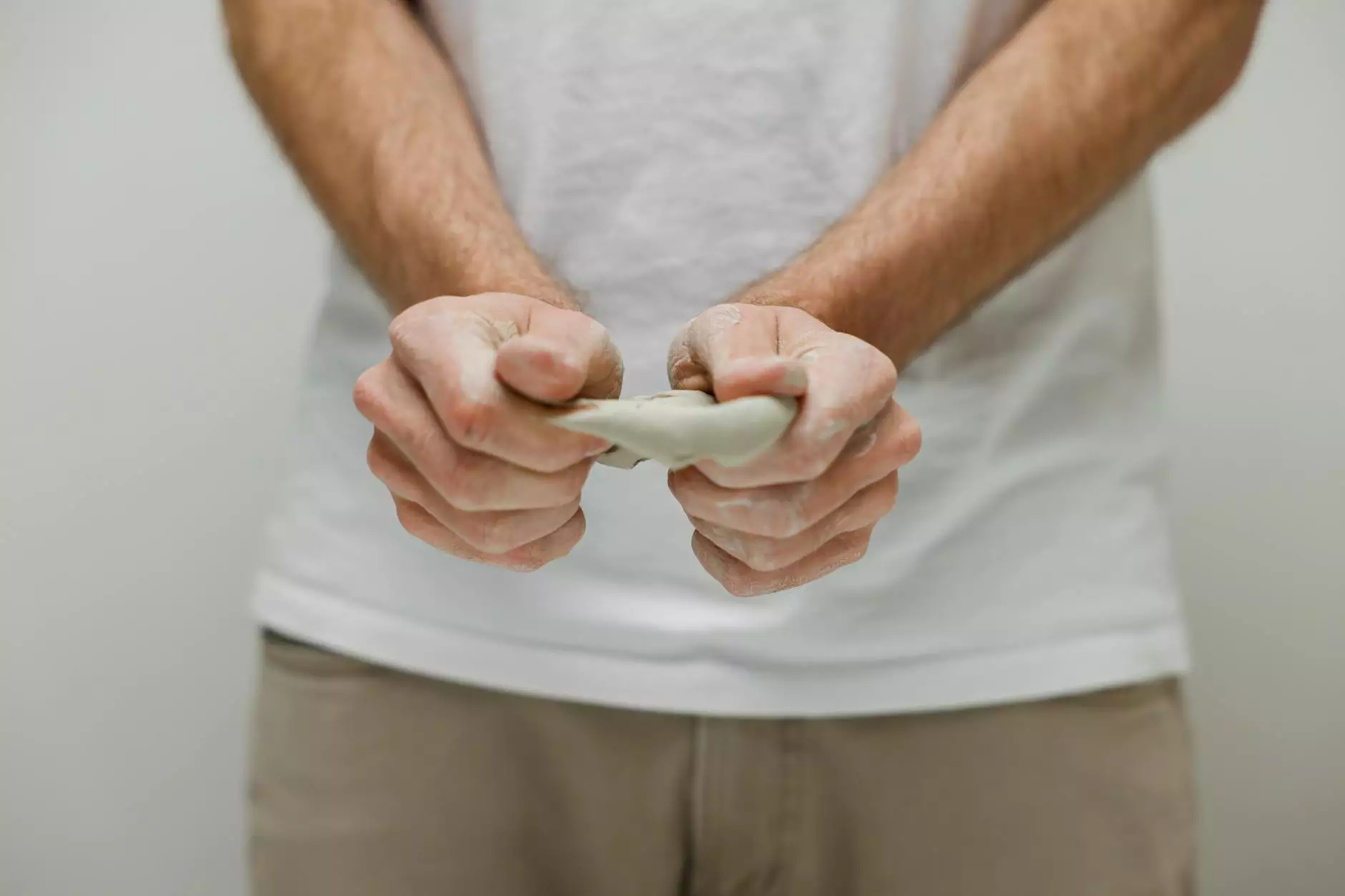
Introduction to Injected Molded Plastic
Injected molded plastic represents a cutting-edge approach in the world of manufacturing, offering unparalleled precision and efficiency. This method involves the creation of complex shapes and designs by injecting molten plastic into a closed mold. As a result, it allows for high-volume production while maintaining the integrity of design. Whether for consumer products, auto parts, or intricate components used in machinery, injected molded plastic is revolutionizing how we think about production.
The Process of Injection Molding
The process of injection molding is intricate yet fascinating. It consists of several crucial steps:
- Design Phase: Engineers create detailed designs using computer-aided design (CAD) software. This step aligns perfectly with the client's visions and specifications.
- Mold Creation: Once the design is approved, molds are fabricated, typically from steel or aluminum. These molds will withstand the high pressure of injection molding.
- Injection: The raw plastic materials are melted and injected into the mold at high temperatures, allowing them to fill in all design details.
- Cooling: The molten plastic cools and solidifies, forming the final product.
- Demolding: After sufficient cooling, the mold opens, and the finished product is ejected.
- Finishing: Final touches are applied, such as trimming excess material, painting, or coating as needed.
Applications of Injected Molded Plastic in Various Industries
Injected molded plastic is not confined to a single industry; its versatility allows it to serve multiple sectors, including:
1. Automotive Industry
In the automotive sector, the demand for lightweight and durable materials is ever-growing. Injected molded plastic plays a vital role in producing interior components, dashboards, and exterior parts, contributing to fuel efficiency and design aesthetics.
2. Consumer Goods
From toys to electronics, injected molded plastic is foundational in manufacturing consumer products. The ability to produce intricate designs at scale means brands can offer innovative and attractive products to their customers.
3. Industrial Equipment
Machinery and heavy equipment often utilize injected molded components. These parts can withstand high levels of stress and wear, making them ideal for operational efficiency. Examples include gears, housings, and connectors.
4. Medical Devices
The healthcare industry intensely relies on injected molded plastic for creating medical devices and supplies. Items like syringes, surgical instruments, and diagnostic equipment are manufactured with high precision and hygienic standards.
Advantages of Injected Molded Plastic
Understanding the benefits of using injected molded plastic is key for businesses considering this manufacturing approach:
- Efficiency: The ability to produce large quantities in a short time reduces per-unit costs.
- Precision: High levels of accuracy in the replication of designs lead to less waste and higher quality products.
- Complex Geometries: Designers can create complex and intricate shapes that would be impossible with other manufacturing methods.
- Material Versatility: A wide range of plastics can be used, providing flexibility in choosing materials based on strength, durability, and cost.
- Reduced Labor Costs: Automation in the injection molding process can significantly lower labor requirements.
Environmental Considerations in Injected Molded Plastic Productions
As sustainability becomes paramount in manufacturing, injected molded plastic processes have evolved. Here are ways the industry is addressing environmental concerns:
- Recyclability: Many modern plastics used are designed to be recyclable, reducing waste.
- Energy Efficiency: Improved systems and machinery innovations are leading to less energy consumption during production.
- Bioplastics: The development of biodegradable plastic alternatives is gaining traction, offering greener options for injection molding.
The Future of Injected Molded Plastic
The future of injected molded plastic appears bright with continuous advancements in technology. Trends to watch for include:
- Advancements in Materials: More robust and sustainable materials are being developed, providing better performance and less environmental impact.
- Increased Automation: Smart factories and automation technologies will further enhance the efficiency of the injection molding process.
- Industry 4.0 Integration: The convergence of digital technologies with manufacturing processes will lead to greater data utilization and IoT applications.
Conclusion
In conclusion, injected molded plastic offers incredible advantages and is integral in modern manufacturing across various sectors. Its capacity for producing precision parts at scale ensures that it remains a cornerstone technology within industries such as automotive, consumer goods, and medical devices. As innovation continues to shape this landscape, businesses that leverage injected molded plastic will maintain a competitive edge in a rapidly evolving market. For those looking to integrate or optimize the use of injected molded plastic, partnering with experienced manufacturers like Deepmould can provide the expertise and capabilities needed to succeed.